Branchen
Fachleute in Entwicklungsabteilungen sehen sich regelmässig mit Fragen konfrontiert, die sich auf die Herstellkosten eines Produkts beziehen. Während sich die Herstellkosten von einem realisierten Serienprodukt aus der eigenen Produktpalette einfach klären lassen, sieht das bei Kosten von Wettbewerbsprodukten, Zukaufkomponenten oder alternativen Konzepten ganz anders aus. Geht es um diese Kostenschätzungen, wird es komplex: Die Herstellkosten eines Mitbewerberprodukts oder die Kalkulation von einem externen Lieferanten lassen sich nicht aus dem eigenen System lesen. Doch was würde es bedeuten, wenn diese Informationen vorlägen und es zudem die Möglichkeit gäbe, diese Kosten zu optimieren? Im Alltag von Helbling wird eine bewährte Methodik genutzt, um diese Prozesse zuverlässig umzusetzen.
Bei der Produktentwicklung kommen unweigerlich Fragen zu den Herstellkosten auf, die Fachleute intensiv beschäftigen können. Klassischerweise sind dies unter anderem diese:
- Wie gut erreichen wir den Zielpreis?
- Benchmark Analyse: Wo stehen die Herstellkosten von unserem Produkt in Relation zum Wettbewerb?
- Wo liegen die Kosten von zugekauften Komponenten? Wie weit sind diese möglicherweise überteuert?
- Welche Vorteile ergeben sich bei einer Produktionsverlagerung?
- Wie wirken sich Stückzahlszenarien aus?
Bei Helbling hat sich ein systematisches Vorgehen bei der Ermittlung und Optimierung von Herstellkosten etabliert. Auf diese Weise konnten Projekte in verschiedenen Branchen bereits erfolgreich aufgegleist werden. Einige Beispiele werden in der Folge im Rahmen der schematischen Abbildungen angeführt.
Schritt 1: Ermittlung der Herstellkosten
Basis ist hierbei, dass mithilfe einer datenbankbasierten Kostenkalkulation die Kostentreiber von bestehenden oder auch neu zu entwickelnden Produkten identifiziert werden. Dazu verwendet Helbling unter anderem das Tool DFMA® von Boothroyd and Dewhurst. Dabei können Kalkulationen anhand von der ersten Konzeptskizzen, in Form von fertig entwickelten 3D-CAD-Daten mit Zeichnungen oder als existierende Baugruppe etwa von einem Mitbewerber durchgeführt werden. Für die Ermittlung der Herstellkosten werden mit dem Kunden zu Beginn die Prämissen der Kalkulation, wie zum Beispiel Fertigungsstandort und Stückzahlen, festgelegt. Diese Angaben sind relevant für die Auswahl der Fertigungshilfsmittel und die Bestimmung des Automatisierungsgrades. Anschliessend können Schätzungen ab Stückzahl „eins“ bis hin zu Millionenstückzahlen durchgeführt werden. Durch die Eingabe von einigen, für die Herstellkosten relevanten Daten, wie etwa Grösse, Komplexität, Material und Herstellmethode, können mit dem Tool die Herstellkosten eines Bauteils ermittelt werden. Ergänzend lassen sich neben der Herstellung von Einzelteilen auch Montage- und Prüfschritte darstellen und abschätzen. Als Ergebnis werden von dem Tool sowohl Teile- und Montagekosten als auch Investitionskosten wie etwa Werkzeugkosten ausgegeben.
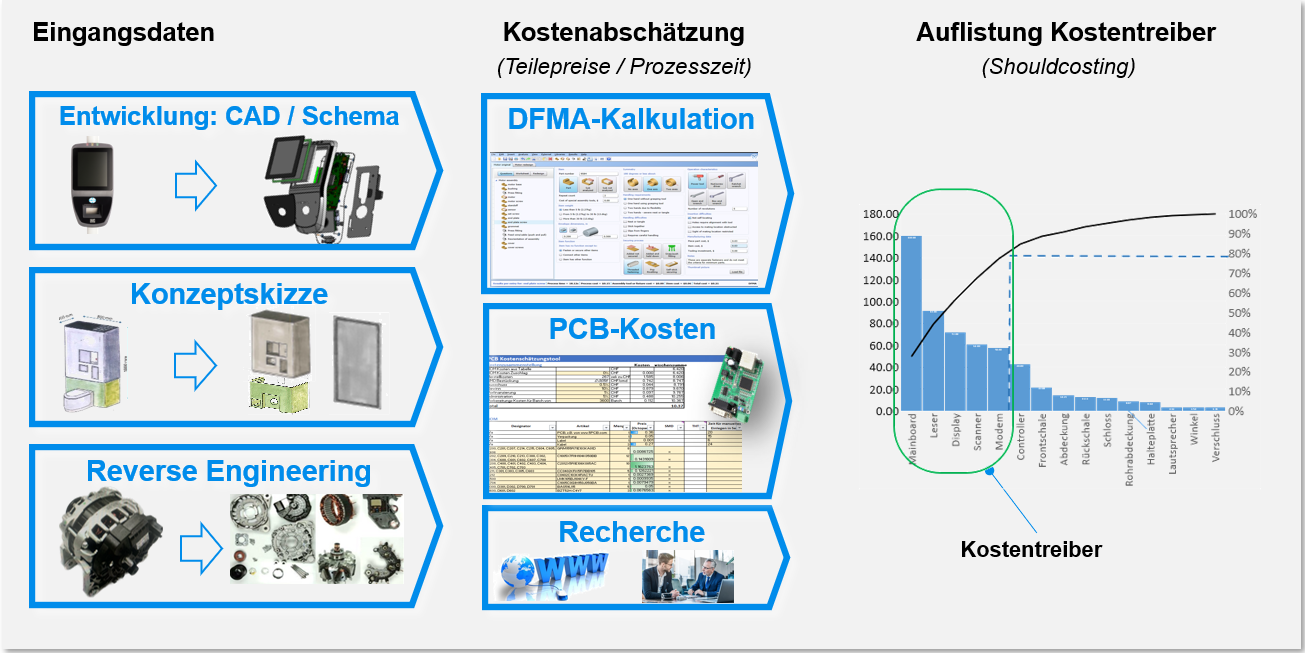
Das DFMA-Tool von Boothroyd and Dewhurst generiert somit sowohl die Teilekosten (Design for Manufacturing) als auch die Montagekosten (Design for Assembly). Damit lassen sich die kompletten Herstellkosten von einem Produkt ermitteln. Die Erfahrungen aus dem Alltag zeigen, dass ergänzend die Kosten für komplexe Zukaufkomponenten zusätzlich recherchiert, angefragt oder durch Expertengespräche in Erfahrung gebracht werden sollten.
Wie in Abbildung 1 grafisch dargestellt, kann die Kostenermittlung mit einer Analyse abgeschlossen werden. Dabei können die ermittelten Kosten von Komponenten, Baugruppen und Prozessen nach ihrer Relevanz ausgewertet werden. Helbling verwendet dabei die Pareto Analyse, in der die Kostentreiber dank der grafischen Darstellung einfach abgelesen werden können.
Auf diese Weise ist einer der wesentlichen Schritte erreicht: Die Herstellkosten eines Produkts sind bekannt und können auf der Ebene von Bauteilen, Baugruppen sowie Montageschritten dargestellt und analysiert werden.
Schritt 2: Optimierung der Herstellkosten
Die Frage des „Wie weiter? “ kann abhängig vom Ergebnis und den Erwartungen diskutiert und individuell beantwortet werden. Sofern die eigenen Kostenerwartungen bereits getroffen werden, ist man an dieser Stelle bereits am Ziel. Möchte man die Kosten optimieren beziehungsweise reduzieren, haben sich verschiedene Ansätze im R&D-Alltag etabliert. Diese sind in der folgenden Grafik qualitativ in Abhängigkeit von Aufwand und Potential dargestellt und im folgenden beschrieben.
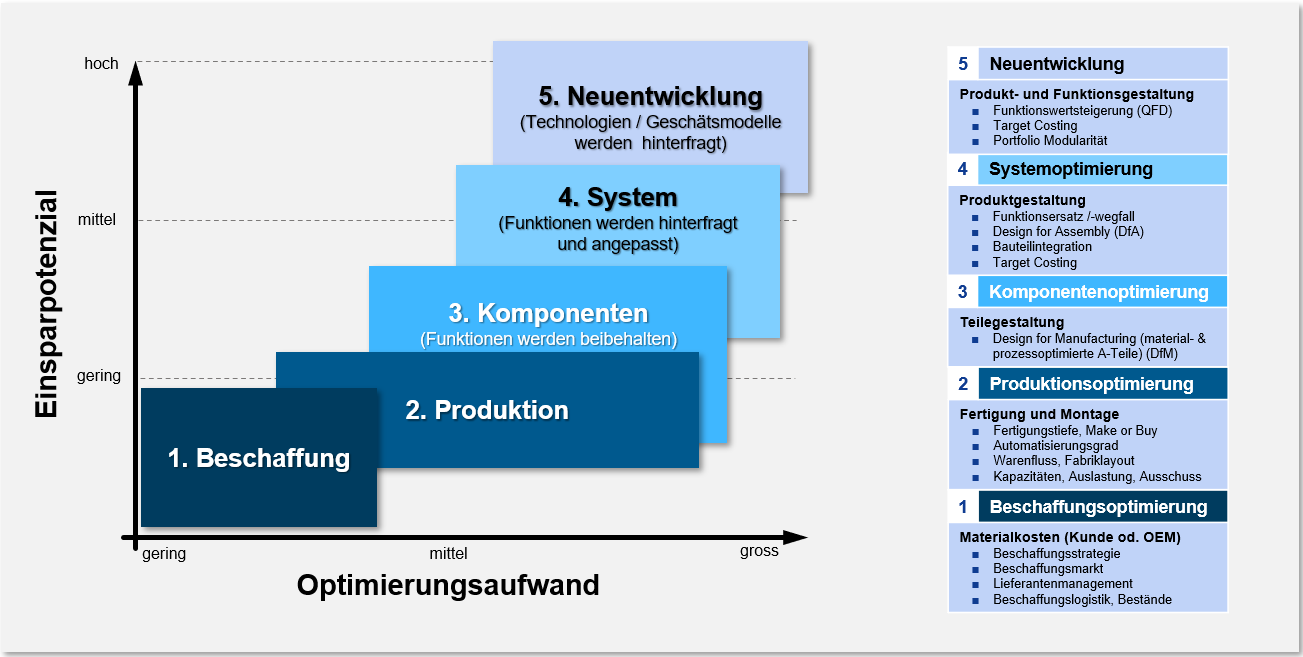
Je nach Herausforderung können Optimierungen in einem oder auch mehreren Bereichen erforderlich sein. Es empfiehlt sich, anspruchsvolle Ziele zu definieren, um den Betrachtungshorizont nicht von vornherein zu sehr einzuschränken. Abstrakt bieten die fünf Stufen aus Abbildung 2 einen systematischen Ansatz der Optimierungsmöglichkeiten. Bei komplexen Produkten können in der Praxis für die unterschiedlichen Baugruppen eines Produkts abhängig vom gewünschten Kosteneinsparziel auch verschiedene Ansätze gewählt werden.
Fünf Ansätze einer Kostenoptimierung:
1. Optimierung der Beschaffung:
Eine Beschaffungsoptimierung bezieht sich rein auf die Lieferanten. Die Teile und das Produkt bleiben unverändert. Hierbei gibt es verschiedene Möglichkeiten:
I. Marktanalyse: Eine Analyse des globalen Beschaffungsmarkts ermöglicht es, günstigere und im Idealfall gleichzeitig qualitativ hochwertigere Lieferanten zu identifizieren. Hierbei kann die in Abbildung 3 dargestellte Beschaffungsanalyse eines Bauteils einen Mehrwert bringen, indem die unterschiedlichen Stundensätze von verschiedenen Ländern für die Kostenoptimierung ausgenutzt werden.
II. Verhandlungsstrategien: Dank der Herstellkostenanalyse sind die theoretisch möglichen Kosten bekannt. Dieses Wissen kann für eine Verhandlung strategisch entscheidend sein, um die besten Konditionen mit Lieferanten auszuhandeln. So ist der Spielraum des Lieferanten deutlich besser abzuschätzen.
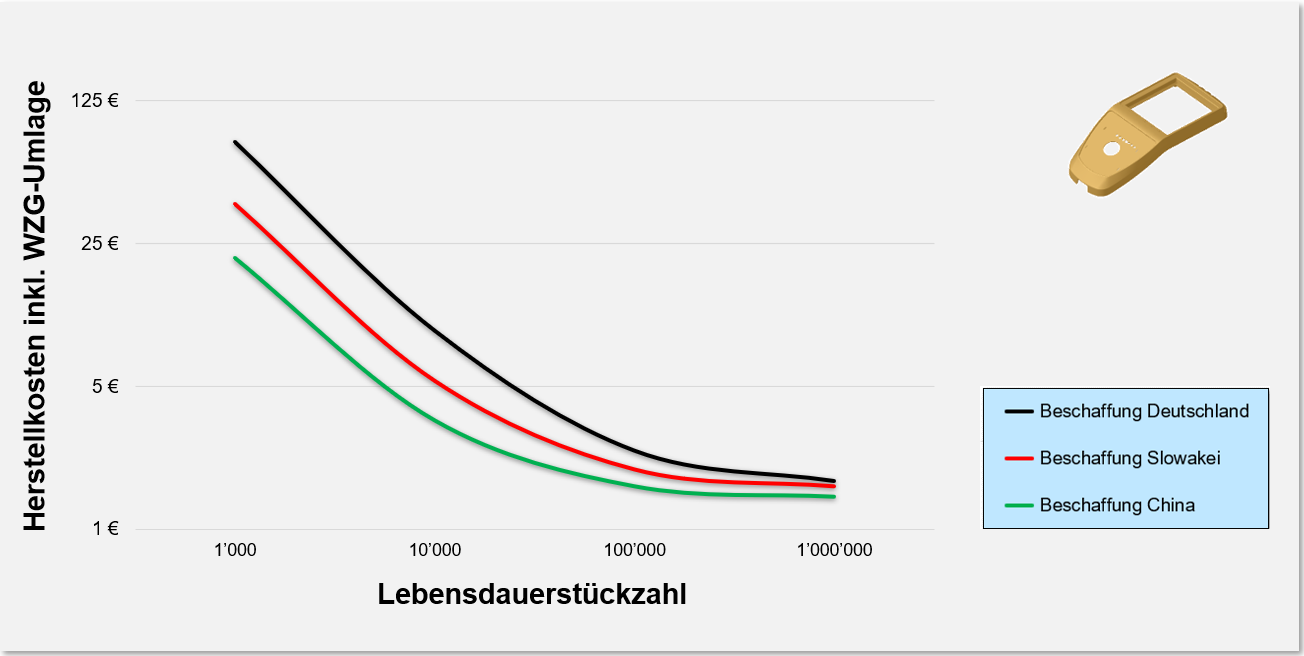
2. Optimierung der Produktion:
Bei einer Optimierung der Produktion werden Montage- und Handling schritte sowie die verwendeten Technologien in der Produktion analysiert. Das Produkt und die Teile bleiben unverändert, es wird lediglich die Effizienz durch das Minimieren von unnötigen Schritten erhöht.
I. Prozessanalyse: Der Produktionsprozess wird detailliert analysiert. Ineffiziente oder überflüssige Schritte können damit identifiziert und gegebenenfalls optimiert werden.
II. Automatisierung: Das Potenzial einer Automatisierung oder einer Erhöhung des Automatisierungsgrads kann ebenfalls mit Hilfe des DFMA® Tools ermittelt werden. Damit können konkrete Einsparungen und der Investitionsbedarf abgeschätzt und verglichen werden.
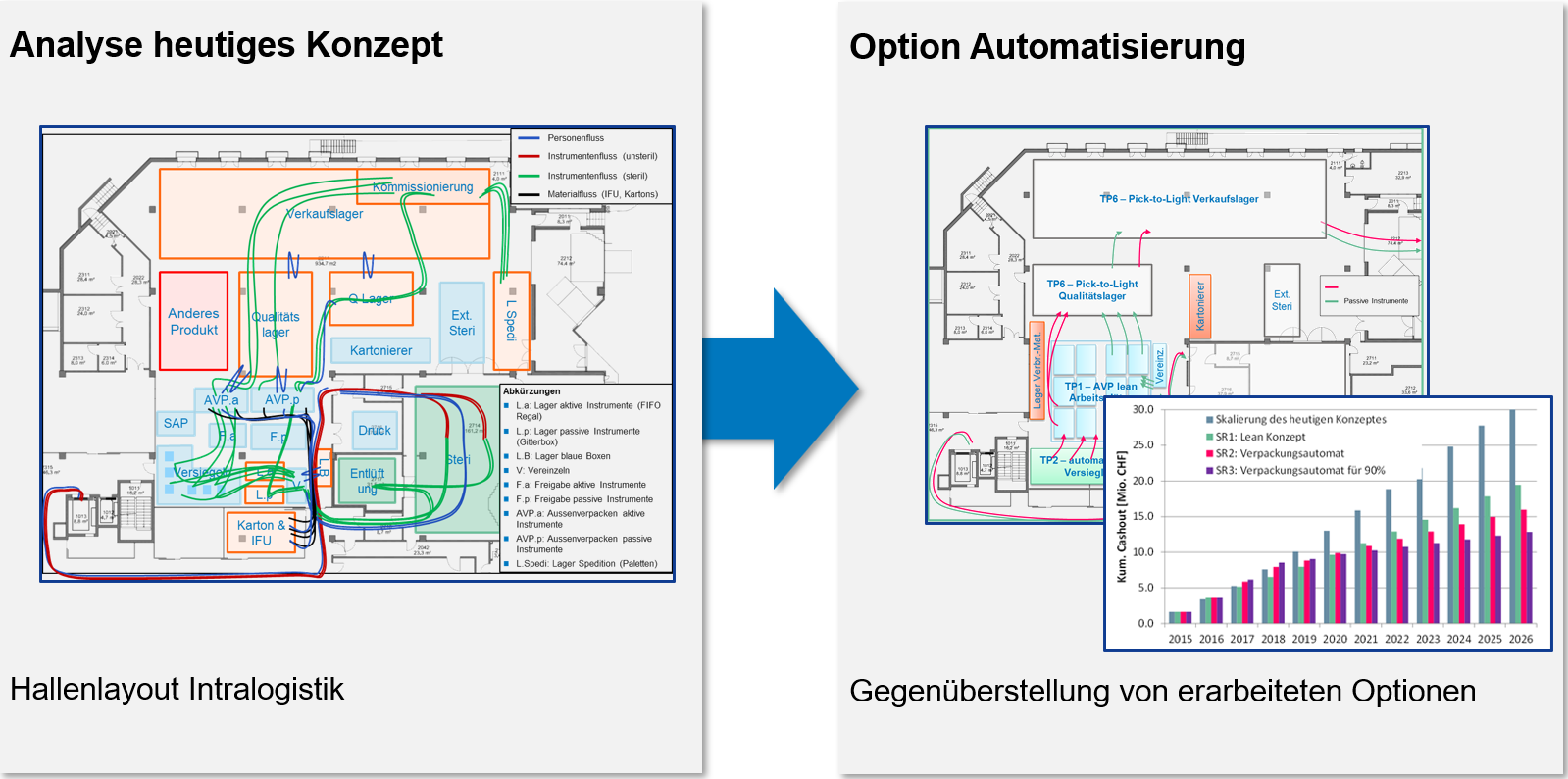
3. Optimierung der Komponenten:
In diesem Schritt werden gezielt einzelne Komponenten optimiert. Je nach Methode ist es möglich, dass einzelne Teile zugunsten geringerer Herstellkosten angepasst werden.
I. Designüberprüfung: Durch die Analyse des Designs werden Verbesserungsmöglichkeiten in Bezug auf Materialverbrauch, Haltbarkeit und Kosten identifiziert.
II. Materialauswahl: Insbesondere bei grösseren und schwereren Komponenten oder bei der Verwendung von teuren Materialien spielen die Materialkosten einen signifikanten Faktor bei den Herstellkosten. Bei der Optimierung gilt es, kosteneffektive und dennoch qualitativ hochwertige Alternativen auszuwählen.
III. Technologieauswahl: Der Herstellprozess kann in Abhängigkeit zur benötigten Stückzahl einen grossen Einfluss auf die Kosten haben. Ein Beispiel hierzu ist in Abbildung 5 gegeben. Das gewählte Bauteil erfüllt jeweils die gleiche Funktion. Das Design wurde für das jeweilige Herstellverfahren angepasst. Die ermittelten Kosten sind abhängig der Stückzahlen für die verschiedenen Herstellverfahren aufgetragen.
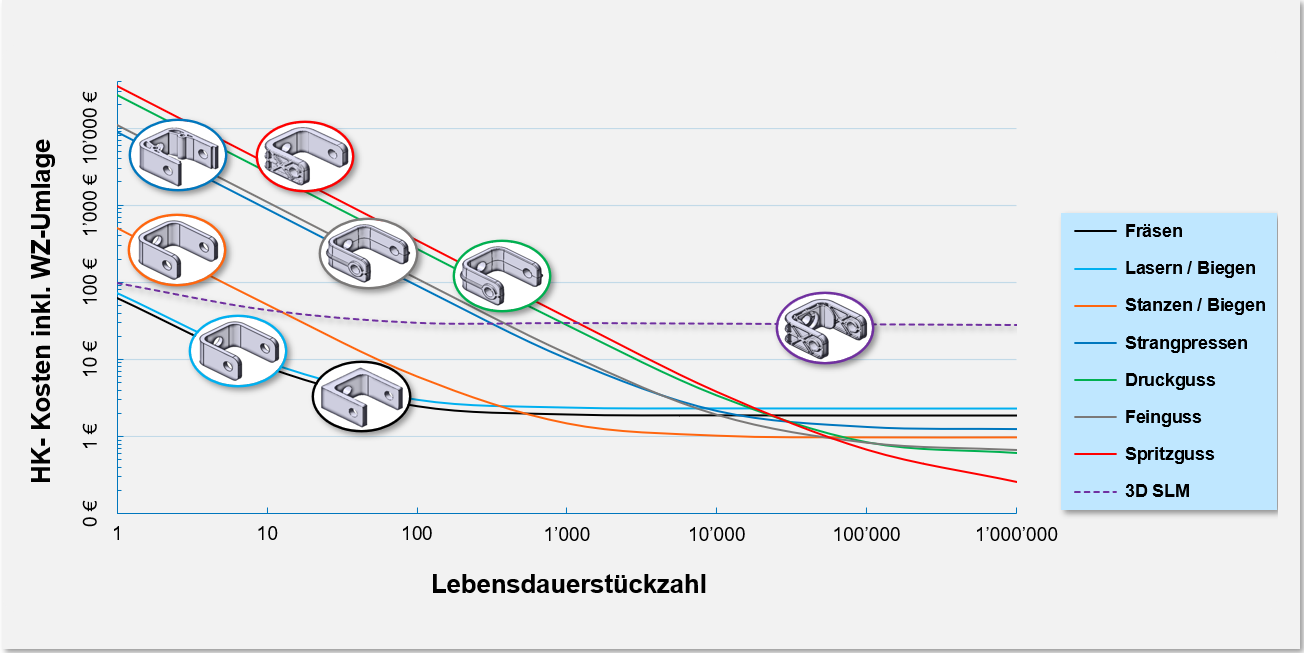
4. Systemoptimierung:
Bei der Systemoptimierung werden komplette Baugruppen analysiert und allenfalls optimiert. Im Idealfall kann damit die Anzahl der Bauteile reduziert und/oder die Montagezeit verbessert werden.
I. Analyse bestehender Systeme: Indem Fachleute tiefgehende Analysen des bestehenden Systems durchführen, identifizieren sie ineffiziente Prozesse oder veraltete Technologien.
II. Bauteileintegration: Durch das Zusammenführen mehrerer Funktionen in einem einzigen Bauteil wird die Anzahl der Bauteile reduziert, womit Material- und Herstellkosten gesenkt werden können. Zusätzlich werden Schnittstellen minimiert, was die Zuverlässigkeit erhöhen kann.
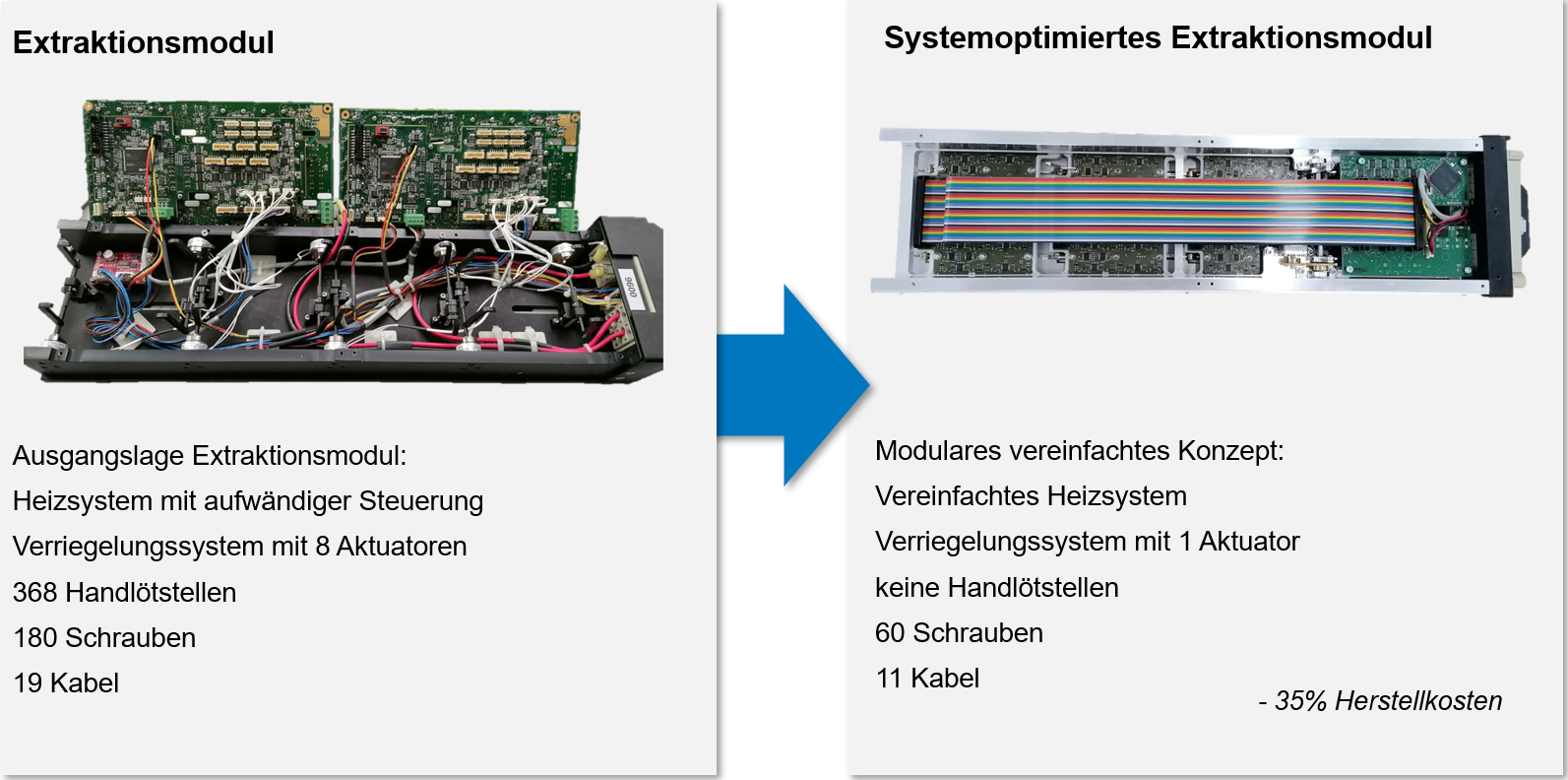
5. Neuentwicklung:
Die Neuentwicklung einer Baugruppe, eines Moduls oder eines kompletten Produkts eröffnet komplett neue Dimensionen bei der Optimierung der Herstellkosten. So konnten bei dem Beispiel aus Abbildung 7 mit einem Wechsel der Sensortechnologie, die Kosten um mehr als Faktor drei reduziert werden:
I. Implementierung neuer Technologien: Durch das Ermitteln und Implementieren von alternativen Technologien kann die Systemeffizienz gesteigert werden. Dies bedingt allerdings, dass grundlegende Eigenschaften geändert werden.
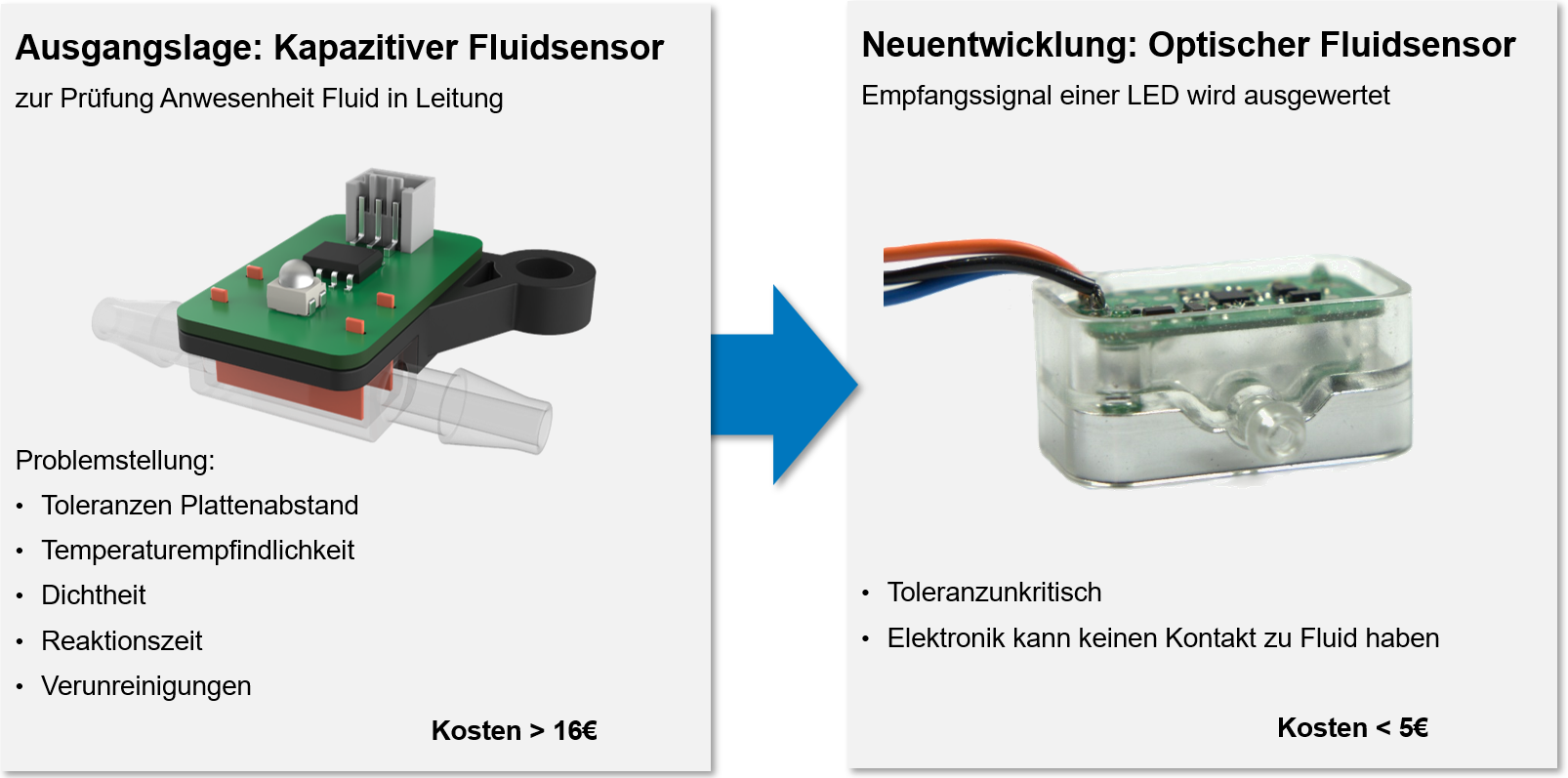
Optimierung oder Herstellkostenreduktion: Das prinzipielle Vorgehen ist meistens ähnlich: Im ersten Schritt werden die Herstellkosten ermittelt. Gemäss dem Paretoprinzip können damit die Kostentreiber ermittelt werden. Anschliessend gibt es verschiedene Ansätze zur Optimierung oder Reduktion der Herstellkosten. Welcher Ansatz in der Praxis der beste ist, muss situativ in Abhängigkeit zur Aufgabenstellung und zum akzeptierten Aufwand entschieden werden.
Zusammenfassung: Kostenkontrolle ist eine Frage der Methode
Datenbankbasierte Kostenkalkulation ist elementar dafür, um Herstellkosten effizient in den Griff zu bekommen. Darüber hinaus steht eine ganze Reihe von Möglichkeiten und Methoden zur Verfügung, um die Kosten zu optimieren. So kann bei der Beschaffung, der Produktion, den Komponenten oder beim System an sich angesetzt werden. Oder es wird der Entscheid gefällt, eine Neuentwicklung zu wagen. Helbling besitzt langjährige Erfahrung darin, Kunden in diesem Prozess zu beraten und zu begleiten.
Autoren: Thomas Rümmelin, Johannes Eckstein
Hauptbild: Helbling