When companies expand or restructure their production capacities, this offers the opportunity to review and optimize existing processes. These often remain unused, despite value stream mapping providing an effective tool for this. At Helbling, this forms the basis of successful factory planning projects and experience shows that this is indeed the case: with a systematic approach and seamless integration in the overall planning process, value stream mapping provides significant support in eliminating bottlenecks and increasing efficiency.
Factory planning as a chance
In order to remain competitive in an increasingly dynamic business world, many companies must adapt processes and production capacities to meet constantly changing customer requirements. At the same time, increasingly complex structures require continuous optimization to ensure profitability in the face of rising cost pressure. Expanding or restructuring production capacities generally offers the ideal opportunity to improve existing structures and processes and increase competitiveness. Helbling has been supporting complex factory planning projects for years in sectors such as medtech or the automotive industry. Customized and interdisciplinary teams use their know-how and experience to support companies with implementing even extensive improvements in factory planning.
The problem of unused potential
Reconstruction or new construction projects often must be performed with a tight schedule and high cost pressure. At the same time, the productivity of the production facilities, which are often operating at their limits, must not be compromised. In reality, existing processes are unfortunately often not reviewed in this context, but instead are transferred unquestioningly in line with the proverb “if it ain’t broke, don’t fix it”. As a result, potential is often not utilized, systems are incorrectly dimensioned, or outdated technology is reinstalled. This causes the productivity of the new site to suffer due to old and inefficient processes, which in turn has a significant negative impact on competitiveness in the long term.
The reluctance to review and rethink existing processes is often also based on the fear of failure due to the challenges associated with change. In addition, many worry about the additional work involved in optimization: faced with tight schedules and high cost pressure, the required resources are often lacking in complex construction projects. Furthermore, project managers are usually not judged by the long-term efficiency of the production processes but by the successful completion of the project. As a result, opportunities are often consciously or unconsciously wasted.
Value stream mapping: The basis for successful factory planning
At Helbling, the review and optimization of processes are an integral part of every factory planning project in order to ensure that the efficiency of new factories is not compromised by old or inefficient processes over many years. Helbling's proven approach based on the VDI 5200 guideline creates transparency in a structured manner and minimizes risks in the planning process. The value stream methodology is often a central element for the systematic assessment and improvement of the relevant processes.
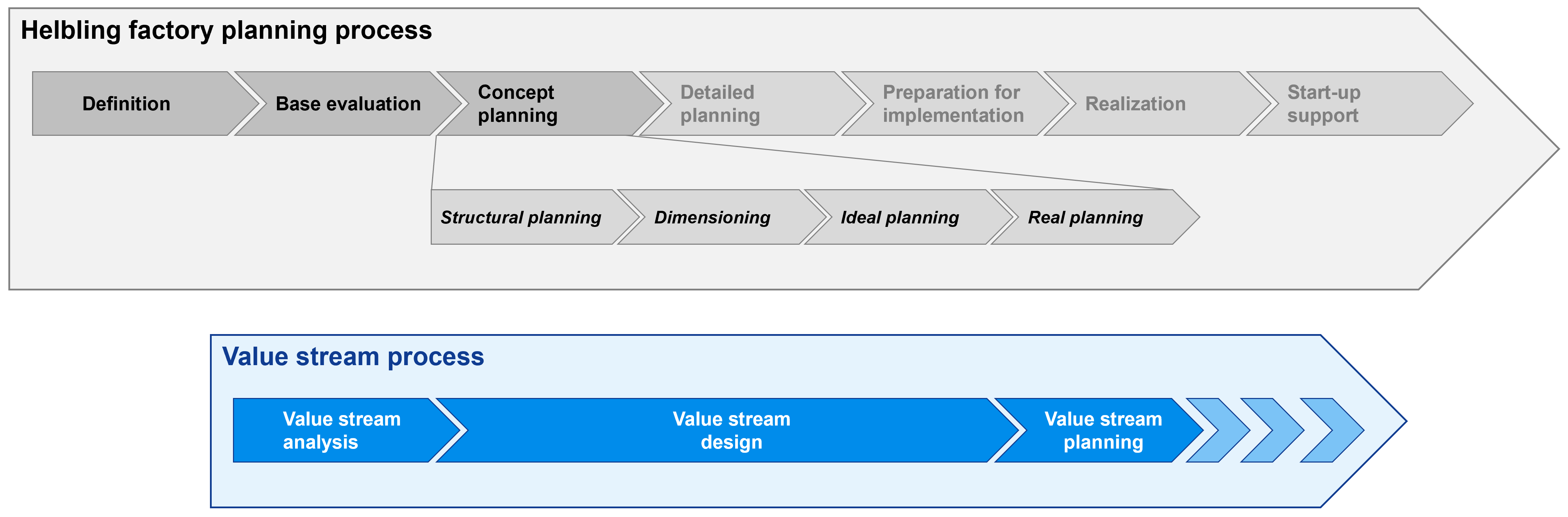
In the first place, a common understanding of the scope and objectives must be created as part of the project definition. In the subsequent base evaluation, the existing processes are evaluated in the value stream analysis in the context of the entire supply chain to identify and visualize inefficient processes (waste).
Based on this, an optimized value stream design is created in the concept planning using predefined design criteria (see Figure 2), which is incorporated into the factory planning project as the basis for value stream planning. The value stream-oriented planning of a new factory helps to focus on the processes that truly add value for a company. This is also reflected, for example, in the required qualification profiles of employees, in which traditional job descriptions such as ‘foreman’ or ‘shift supervisor’ are replaced by ‘value stream manager’.
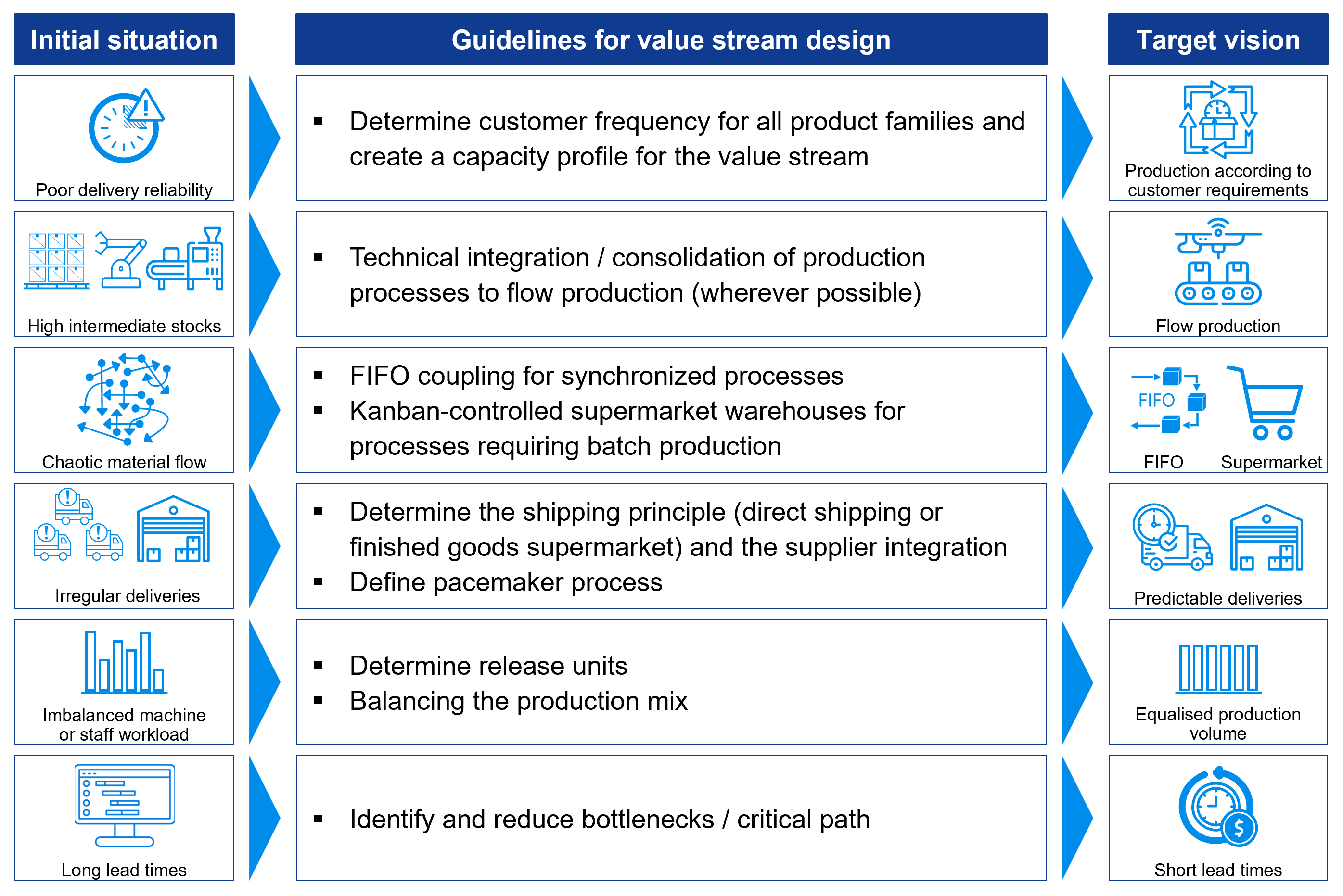
Added value through software-supported value stream mapping
In addition to traditional value stream analysis with pen and paper, specific software tools are available today that can be used to analyze and optimize value streams much more efficiently. At the same time, the data is backed up and changes can be made and tracked at any time. This makes it quick and easy to make statements about different processes and scenarios and quantify the expected impact on the overall system. Helbling usually uses the specialized tool Polaris VSM.
Summary: Taking advantage of opportunities with value stream-oriented processes
With its structured recording and evaluation of processes, value stream mapping rightfully plays a prominent role in the systematic optimization of factories and processes. It makes a significant contribution to increasing efficiency and eliminating bottlenecks and offers a convincing cost-benefit ratio. Further advantages also lie in the fact that it is intuitive to use, offers comprehensible documentation, and can be seamlessly integrated into planning processes. When used consistently in factory planning, it forms a cornerstone for the design of an optimized factory. This helps to save costs, reduce space and, in the long term, increase performance and ensure competitiveness. Companies that successfully implement and live by the methodology initiate a sustainable process and establish a culture of continuous improvement. Helbling has many years of experience in this area and has been able to accompany many clients on their journey.
Authors: Wolfgang Yorck, Matthias Schmid
Main Image: Midjourney