In collaboration with you, we perform process failure modes and effects analyses (PFMEA). This allows us to identify and evaluate the effects of possible failure modes of subsystems, assemblies, components, or functions due to errors during assembly and part production. In addition, we define measures to counteract these.
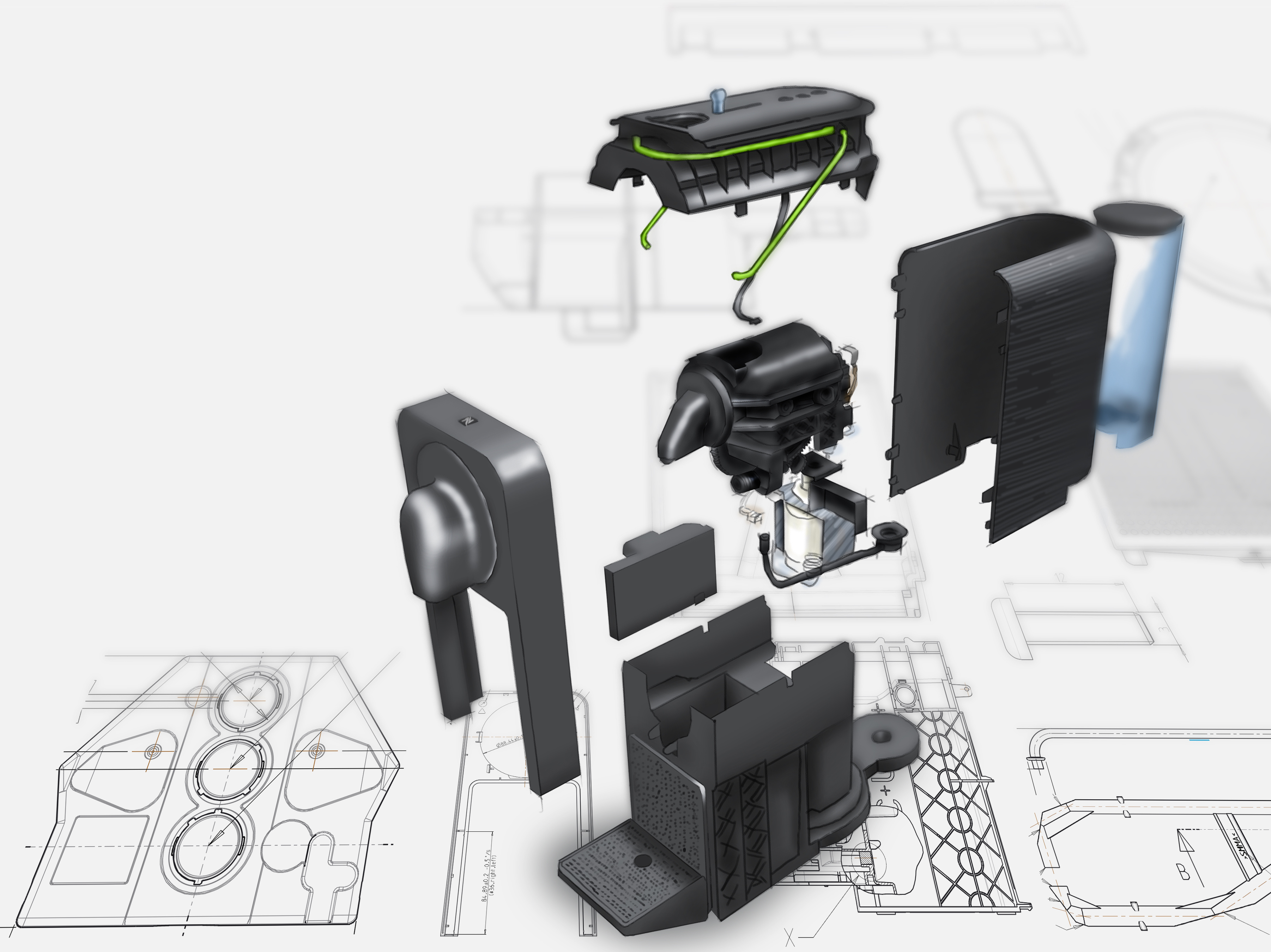
service
Design Transfer
Design transfer is the process by which the development results are transferred to production in a coordinated manner. In design transfer, we ensure that production has all the information needed to manufacture the product according to the specification.
The development department has the task of developing and specifying products that deliver the promised benefits and minimize the product-related risks for users or patients. Production has the task of reliably manufacturing the products according to these specifications. Purchasing has the task of procuring materials, individual parts, assemblies, or entire devices that meet the requirements.
To avoid development loops and to save time and costs, this must be done with cooperation between development, production, and purchasing. The earlier the collaboration starts, the lower the risk for the project.
Core services
Process FMEA
Design for manufacturing
and assembly (DFMA)
and assembly (DFMA)
In DFMA, we support you, for example, at the part level, with the definition of injection points and ejectors for plastic parts. In the case of printed circuit boards, for example, you can count on us for any necessary optimization of the layout for production equipment. We finalize the technical requirement specifications, the design for the manufacturing process, and the assembly process.
Production verification tests
In production verification testing, we assess parts, assemblies, and equipment from pre-series and pilot series production. Finally, input is provided for definition of in-line or end-of-line test equipment.
Design transfer plan in the regulated area (Medtech)
We assist you in creating and implementing a design transfer plan that describes the transition of a product design from development to production. This includes elements such as the following:
- Identifying the quality-critical parameters of the product design. These are features or characteristics of the product that must meet certain standards in order for it to function correctly.
- Development of the manufacturing process. This includes determining the required materials, the necessary manufacturing equipment, and the production layout.
- Validation of the manufacturing process. This involves running a small batch of products through the process to ensure that it is suitable for reproducibly manufacturing the products according to specification.
- Training of production personnel. This includes providing the necessary instructions, procedures, and tools so that the personnel can successfully manufacture the product.
- Monitoring and adjustment of the manufacturing process. This ensures that the product is manufactured to the desired quality standards on a continuous basis.
Design transfer report in the regulated area (Medtech)
We are at your side to support you with preparing a design transfer report. This helps those involved such as management, clients, and regulators to understand the results of the process and evaluate the effectiveness of the design transfer. The report serves as documentation of the design transfer process. The report includes but is not limited to the following elements:
- Overview of the product design, purpose, technical specifications, and performance requirements of the product.
- Description of the steps for transferring the product design to production, including testing and quality control procedures.
- Outlining potential risks and hazards related to the design transfer process and mitigation measures.
- Information on the resources required for the design transfer process, such as personnel, equipment, and materials.
- Timeline for the design transfer process, including key milestones and deadlines
- Results of the design transfer process, including issues encountered.
- Conclusion with recommendations based on the results of the design transfer process, including opportunities for improvement.
In collaboration with you, we perform process failure modes and effects analyses (PFMEA). This allows us to identify and evaluate the effects of possible failure modes of subsystems, assemblies, components, or functions due to errors during assembly and part production. In addition, we define measures to counteract these.
In DFMA, we support you, for example, at the part level, with the definition of injection points and ejectors for plastic parts. In the case of printed circuit boards, for example, you can count on us for any necessary optimization of the layout for production equipment. We finalize the technical requirement specifications, the design for the manufacturing process, and the assembly process.
In production verification testing, we assess parts, assemblies, and equipment from pre-series and pilot series production. Finally, input is provided for definition of in-line or end-of-line test equipment.
We assist you in creating and implementing a design transfer plan that describes the transition of a product design from development to production. This includes elements such as the following:
- Identifying the quality-critical parameters of the product design. These are features or characteristics of the product that must meet certain standards in order for it to function correctly.
- Development of the manufacturing process. This includes determining the required materials, the necessary manufacturing equipment, and the production layout.
- Validation of the manufacturing process. This involves running a small batch of products through the process to ensure that it is suitable for reproducibly manufacturing the products according to specification.
- Training of production personnel. This includes providing the necessary instructions, procedures, and tools so that the personnel can successfully manufacture the product.
- Monitoring and adjustment of the manufacturing process. This ensures that the product is manufactured to the desired quality standards on a continuous basis.
We are at your side to support you with preparing a design transfer report. This helps those involved such as management, clients, and regulators to understand the results of the process and evaluate the effectiveness of the design transfer. The report serves as documentation of the design transfer process. The report includes but is not limited to the following elements:
- Overview of the product design, purpose, technical specifications, and performance requirements of the product.
- Description of the steps for transferring the product design to production, including testing and quality control procedures.
- Outlining potential risks and hazards related to the design transfer process and mitigation measures.
- Information on the resources required for the design transfer process, such as personnel, equipment, and materials.
- Timeline for the design transfer process, including key milestones and deadlines
- Results of the design transfer process, including issues encountered.
- Conclusion with recommendations based on the results of the design transfer process, including opportunities for improvement.
Our Further Services
Services | Product Development
Detailed Design
Services | Industrialization
Design Verification
Services | Industrialization
Experimental Verification, Testing, and Proof of performance
Services | Product Development
Idea Finding & Conception
Services | Product Development
Industrial- & UX-Design
Services | Ideation
Innovation Pre-Projects
Services | Technology Development
Predevelopment
Services | Ideation
Product Vision & Scouting
Services | Product Development
Project Management
Services | Product Development
Software Development
Services | Technology Development
Solution Search, Modeling & Simulation, feasibility analysis
Services | Sustainability
Sustainability Engineering
Services | Product Development