Railway vehicles are usually designed to have a service life of around 40 years. About halfway through this, the technology and equipment must be updated to make railway vehicles safer, more comfortable, and more energy efficient. For example, this can be achieved by installing modern drive systems, improved brakes, new interior fittings, barrier-free access, or by integrating information and communication technologies. Measures to extend the lifespan of rail vehicles conserve resources and are usually more economical than purchasing new ones. They are therefore also advantageous in terms of sustainability. Helbling has implemented many extensive projects in this field in the past. A methodical and interdisciplinary approach is required for this to be successful.
Railway vehicles can be used for longer than originally intended. However, this requires renewal. In this context, Helbling distinguishes between four measures to extend the lifespan:
1. Modernization:
The aim here is to extend the usage while adding enhancements. This includes measures to improve known weak points and passenger comfort, reduce operating costs and resource consumption, increase reliability, and ensure operability.
2. Conversion:
An existing vehicle is meant to fulfill a different function and is converted for this purpose. One example is providing diesel-powered vehicles with an electric drive to contribute to decarbonization. In Switzerland, this mainly relates to company vehicles and construction machinery as passenger trains are already powered by electricity.
3. Renovation:
If damage occurs to several vehicles in a fleet and similar damage is to be expected in other vehicles from this fleet, the cause must be found and a permanent solution implemented.
4. Repair:
After damage caused by long-term use or an accident, the original function is restored. This may be in a different version to the original if necessary. An example is a cast component that is replaced by a welded structure due to a lack of mold.
Helbling has already worked on these types of projects with various customers. To give just one example: Tm 232 rail tractors were converted to Xrotm 491 snow blowers for Swiss Federal Railways SBB.
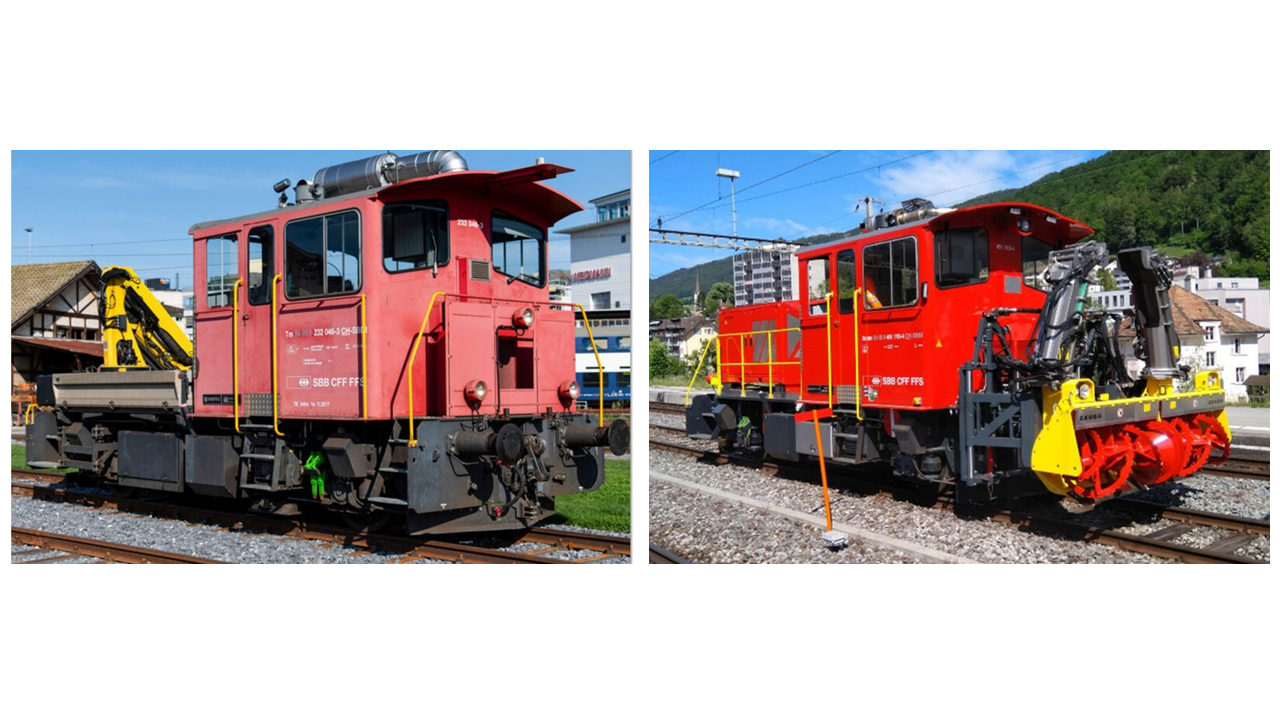
A phased approach ensures project success
No matter how different the individual projects at Helbling are, they all start with thorough implementation of the requirements and feasibility phase. This approach contributes significantly to the project's subsequent success and prevents nasty surprises in future phases. The example of cracks in the vehicle structure shows this well: the crack can be welded shut or reinforced with a plate. This resolves the issue in the short term but leaves the question of cause unanswered. The result is the appearance of new cracks in future that require much greater effort to repair.
Requirements phase sets the framework
The fundamental cornerstones of the project are defined in the requirements phase. Answers to the following questions are useful:
- What should be achieved and within what time frame?
- Which vehicles are available?
- Who are the stakeholders in the project (internal/external)? And what are their responsibilities?
- To what extent is the planned work relevant for approval?
- Which standards, laws, regulations, etc. must be met?
Particular attention must be paid to the topics of stakeholders, approval, standards, laws, and regulations. The wheels of public associations and licensing authorities turn at their own pace and have their own rules of procedure. Standards, laws, and regulations cause additional effort when implemented and verified later. If changes to the regulations are foreseeable during the project period, the way in which they will be handled must be clarified.
The feasibility phase lays the foundations
The feasibility phase primarily concerns creating a solid foundation for the project, both technically and economically.
In this context, the condition of the vehicles is examined and their suitability for the planned task is checked. Additional questions also need to be answered, such as repairing corrosion damage or removing asbestos. The weight and center of gravity of the vehicles are subject to restrictions that must be observed during conversion. To clarify the feasibility, work steps are described, risks are identified, and the procedure for reducing them is sought. When procuring purchased parts, long lead items may have to be considered. For approval, early coordination with the approval authorities can also make sense.
The plan is created after these clarifications, with the rough costs and dates being vital. The project organization documents those involved and their areas of responsibility. Planning also includes the availability of the individual vehicles for the conversion as well as the required facilities and conversion personnel.
External support brings added value
For this complex process, it makes sense for vehicle owners to engage an external engineering service provider such as Helbling for many reasons:
- A company’s own employees are absorbed by their day-to-day business.
- The view from outside prevents operational blindness.
- There is a lack of internal experience in performing such projects.
- The customer can obtain in-depth specialist knowledge in all disciplines.
- The project receives a price and a clear scope of delivery.
- The size of the project team can be varied over the duration.
Summary: vehicles stay on tracks longer with experience, multidisciplinarity, and a phased approach
The complexity of lifespan-extending projects for rail vehicles is due to the high degree of interdependence between the different aspects and their fine-tuning. It is absolutely essential that different disciplines work closely together to implement this successfully. Helbling relies on experts in the relevant areas and provides experience in project management, as these projects require a holistic approach.
Autors: Martin von Wartburg, Jörg Bellingen, Dietmar Uebelmann
Main Image: Montreux Oberland Bernois Railway