Industries
Sustainable cost savings instead of cash flow-driven actionism
The days of "simple" savings levers are over. Companies can no longer focus solely on reducing unit costs through low-cost country sourcing. Resilience, quality, sustainability and customer satisfaction are becoming increasingly important due to current global developments. It is important to face up to this - and ultimately to keep an eye on the key financial figures. This is a complex undertaking that requires a structured, holistic approach and the early involvement of all relevant people.
It's still all about costs ... but the path has changed!
As companies and private individuals we experience on a daily basis, how economic and political developments are shaping a complex scenario of increasing uncertainty at a global level. Trade conflicts, geopolitical tensions, a pandemic and the effects of natural disasters have permanently changed the conditions. Global supply chains have been disrupted and continue to be shaken. The consequences of these shocks are economic problems, from job losses to supply shortages and bottlenecks.
In this complex situation and due to consequences such as increased energy costs in particular, cost reductions are right at the top of the agenda for today’s companies. However, pure cost-cutting and short-term measures run the risk of having unintended, problematic consequences along interlinked supply chains. Furthermore, despite all cost reductions, the ability to react flexibly to changes and create resilient framework conditions must be maintained - a complex undertaking.
Diverging goals and interests not only lead to disagreements, they often torpedo the results of measures along the supply chain
Especially when it comes to achieving savings targets, the focus of everyone responsible is on their own area and the potential that is supposedly quick and easy to exploit. But appearances are deceptive - short-term savings through quick measures without sufficient involvement of all relevant stakeholders will have unforeseen effects elsewhere and lead to additional costs and increased effort.
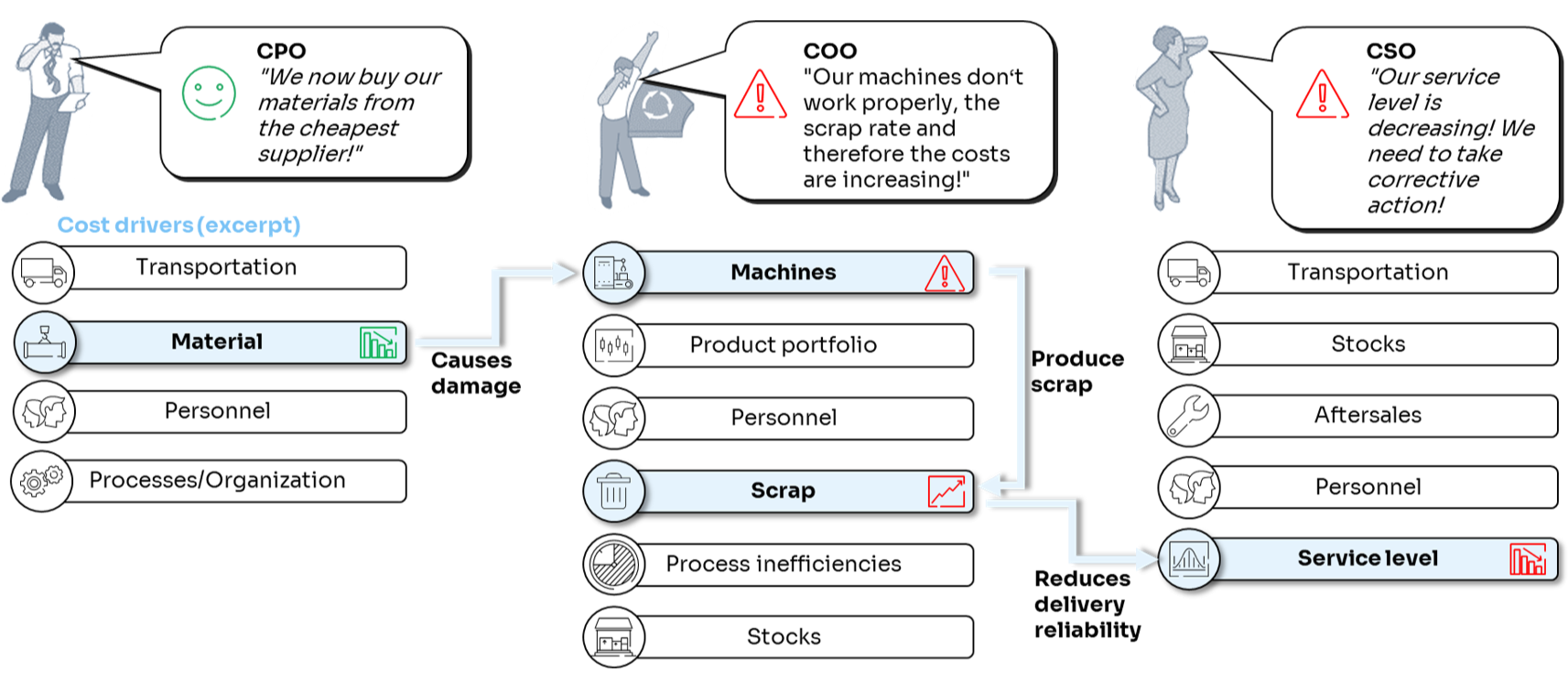
It is essential to synchronize the relevant areas and departments in the company in order to pull together in the same direction - the direction of holistic cost optimization.
As part of our Supply Chain CostSync approach, we at Helbling support you in analyzing and evaluating these effects in advance, involving relevant stakeholder groups at an early stage and thus focusing your efforts on the measures that promise real cost savings - and do so sustainably.
Escape the endless loop with end-to-end measures
If measures, especially those aimed at reducing costs, are implemented in silos and without coordination, there is a risk of resulting problems elsewhere in the company. For example, savings on important raw materials can lead to quality problems and therefore increased costs due to rejects in production if this changeover has not been backed up by sufficient testing and involvement of the engineering teams. The process then starts all over again and corrective measures have to be taken. The repeated design and implementation of such measures entails an enormous amount of effort. Focus this effort on those measures that bring real and sustainable savings - and are not a flash in the pan.
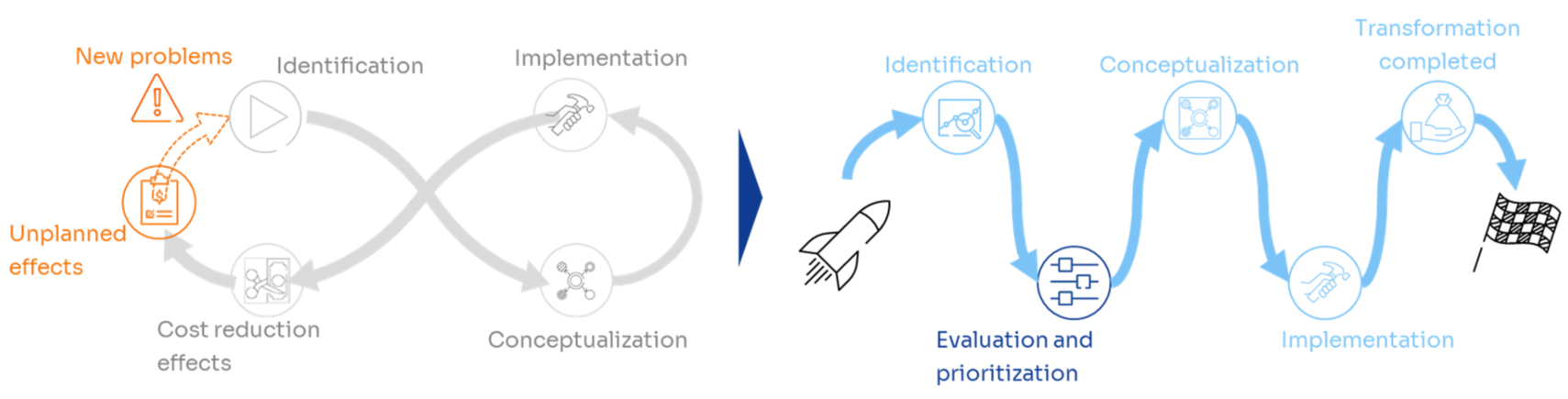
As part of our proven approach, each measure is analyzed in terms of its impact. The measures are then evaluated with regards to their end-to-end usefulness and prioritized for implementation. During conceptualization and implementation, all relevant stakeholder groups affected by a certain measure are identified at the beginning and consistently included throughout the process.
This results in an outcome whose impact on the supply chain is transparent and has been agreed with all relevant stakeholders.
Our 6 concrete steps for end-to-end cost optimization
Are your key financial figures pointing to problems, but you are wondering what the cause of increased costs is? Do you find silo thinking in your company? With the following steps, we can help you break down these silos and optimize costs effectively:
1. Create transparency
Data transparency is the basis for any cost optimization measure. We get to the bottom of the causes and uncover clear reasons for increased costs. At the end of step 1, you will receive a complete picture of the status quo - underpinned by facts and figures.
2. Identification of opportunities and potentials for cost optimization
The transparency created enables identifying problems and thus concrete potentials and deriving measures. Do different plants source the same materials from different suppliers? Requirements can potentially be harmonized and thus material costs optimized.
3. Deep dive into each identified measure - evaluation of impact, effort and risk
Not every identified potential can be easily converted into a measure and implemented right away. There may be a valid reason behind the different suppliers for the same material. For example, is there a delivery time restriction or does the cheaper supplier not have sufficient capacity? The measures are reviewed and evaluated with the involvement of all relevant stakeholders.
4. Prioritization of selected measures for implementation
Not all measures identified and deemed sensible can be implemented immediately. Do individual measures require a certain lead time? Are measures interdependent? Does the company have the resources and capacity to implement them? All such questions must be answered first and considered when drawing up the roadmap.
5. Conceptualization of the measures - development of a detailed plan and identification of relevant stakeholders
This is where the measures are worked out in detail. Who needs to be involved in the implementation? What timetable is sensible and realistic? What are the specific to-do's? How can the success be measured? As soon as these questions have been answered, the detailed implementation plan can be drawn up and agreed.
6. Implementation of the measures and further training of the teams
We do not just deliver ideas - we also tackle them together with our client. In close cooperation with your teams, we implement the defined measures and ensure cost optimization tracking and reporting. At the same time, we train your employees "on-the-job" in the methods and tools used and offer training if required.
Cost optimization with Helbling - across all levels
Our expertise does not end at the boundaries of supply chain and operations. Our experts in the areas of finance, transformation & turnaround management and M&A also support you beyond this in the holistic optimization of earnings and costs throughout the company and the sustainable improvement of profitability.
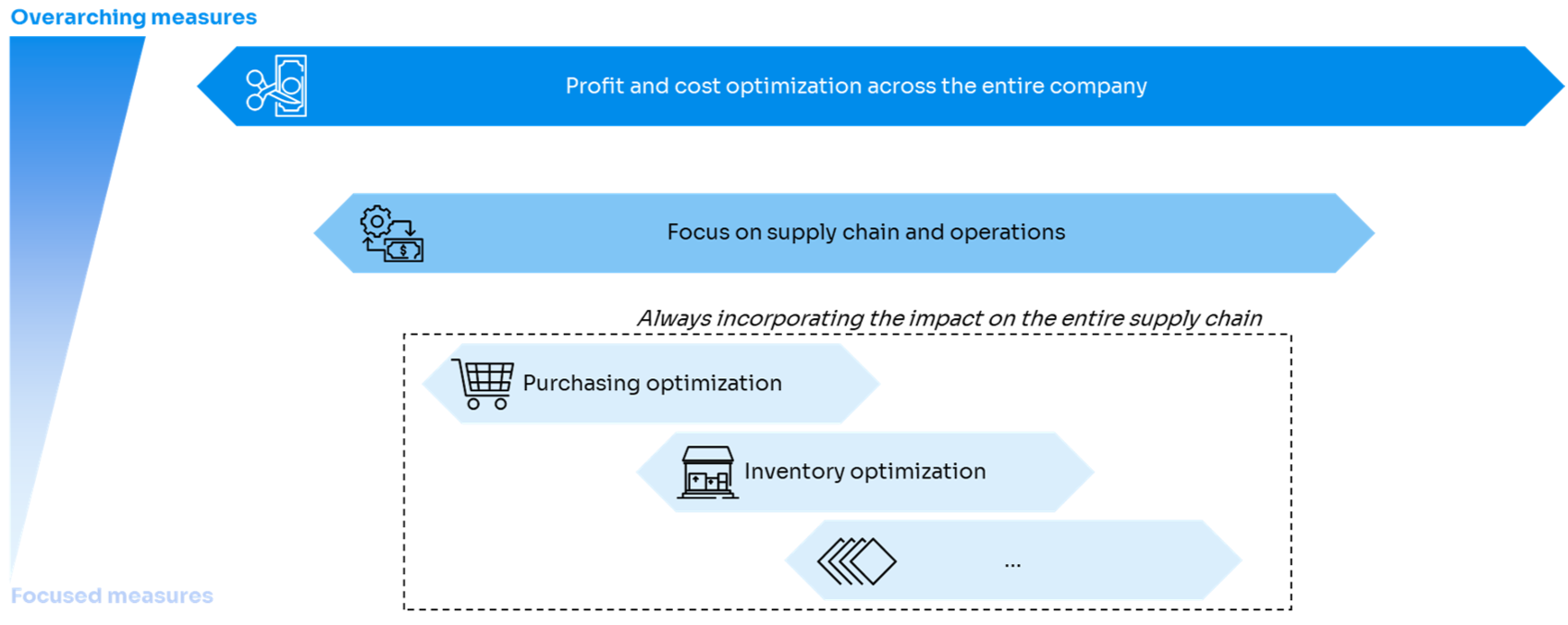
Success stories
Our approach has proven its worth with customers from different industries and business models and has reliably delivered significant cost optimization.
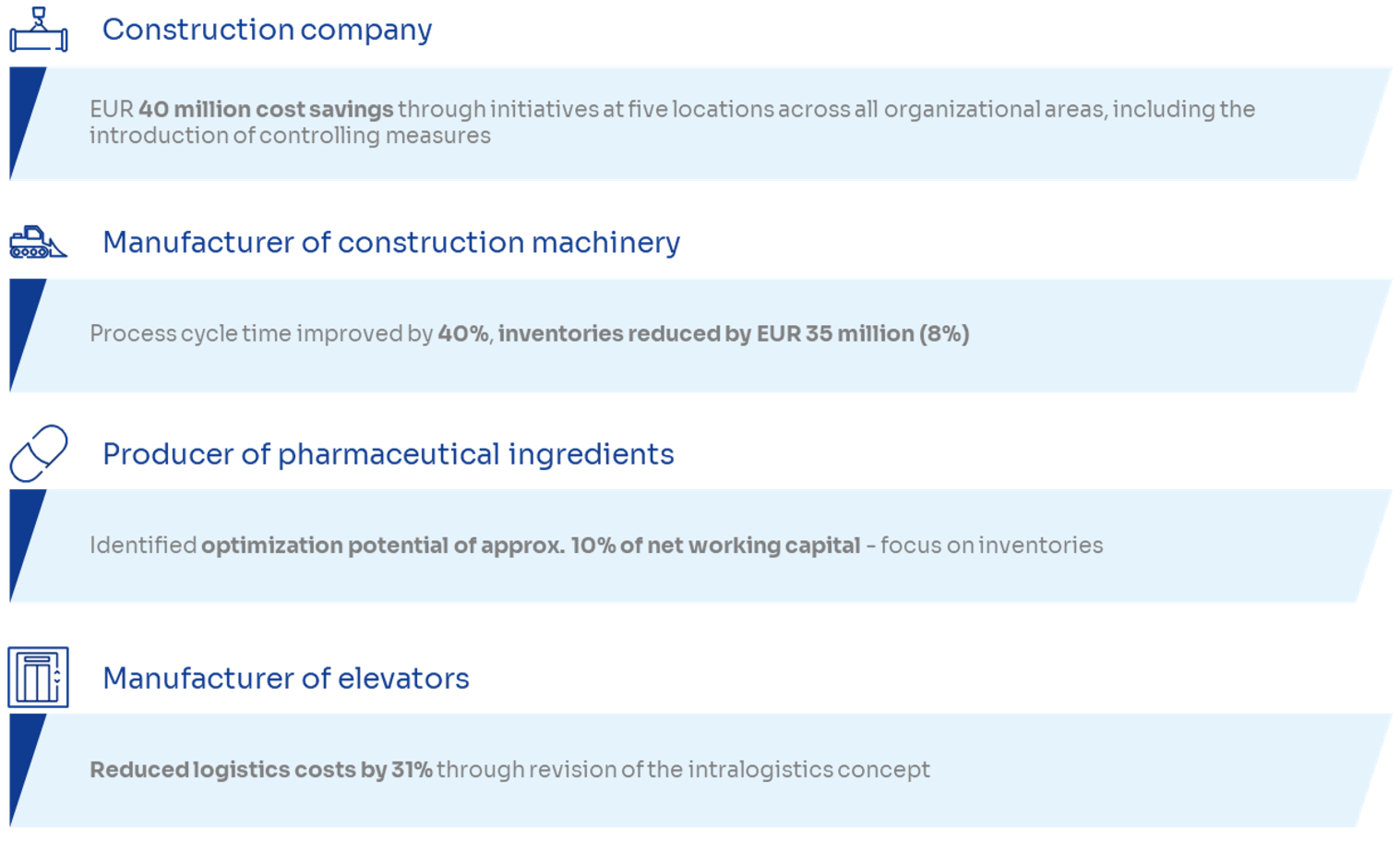
Conclusion
The days of "simple" cost-cutting measures - such as outsourcing to the Far East or reducing of stock levels to the maximum - are over. However, optimized costs and maximum efficiency are more important than ever in the current situation. In order to cope with this in the long term, it is essential that all areas of the company are involved in order to move in the same direction together.
Synchronize your company - we will support you.