In the milling industry, there is usually no way around the decades of experience of master millers. With the intelligent mill E3, Bühler is making the leap into the digital age, where fully autonomous mills with remote monitoring and robust control will be standard practice in the future. For the development of the grinding system’s feed controller, Bühler turned to Helbling's expertise and experience in this area. Anchored in the field of robotics, the example shows how their transfer to other fields and industries creates substantial value.
"What we have in operation here today marks the beginning of a new era in flour milling. We can digitally monitor all our processes through the SmartMill," says Mike Peters, Managing Director at Whitworth Bros. Ltd. and one of the first operators of the E3 smart mill (Figure 1). With this mill, Bühler, the global market and technology leader for milling equipment based in Uzwil in Switzerland, is introducing digitalization on a large scale to an area that is traditionally based on knowledge and craftsmanship that has been passed down through generations. The designation "E3" refers to the three efficiency dimensions of space, time, and energy that the new mill concept allows: exceptionally compact mills that can be set up rapidly and operated in an energy-efficient manner. Another objective is to achieve autonomous operation of the mill. To this end, thousands of data points allow seamless digital monitoring of all processes in the mill and open up new possibilities in quality assurance, process optimization, and operation that previously would have been mere figments of the imagination.
An essential prerequisite for autonomous operation and consistently high quality in the grinding process is a robust control system. In the context of grinding, this means that the product enters the grinding gap consistently and across the entire width, regardless of irregularities in the feed. For this purpose, the feeding module (Figure 2) is equipped with a sophisticated multi-variable control system, which Helbling was commissioned by Bühler to develop.
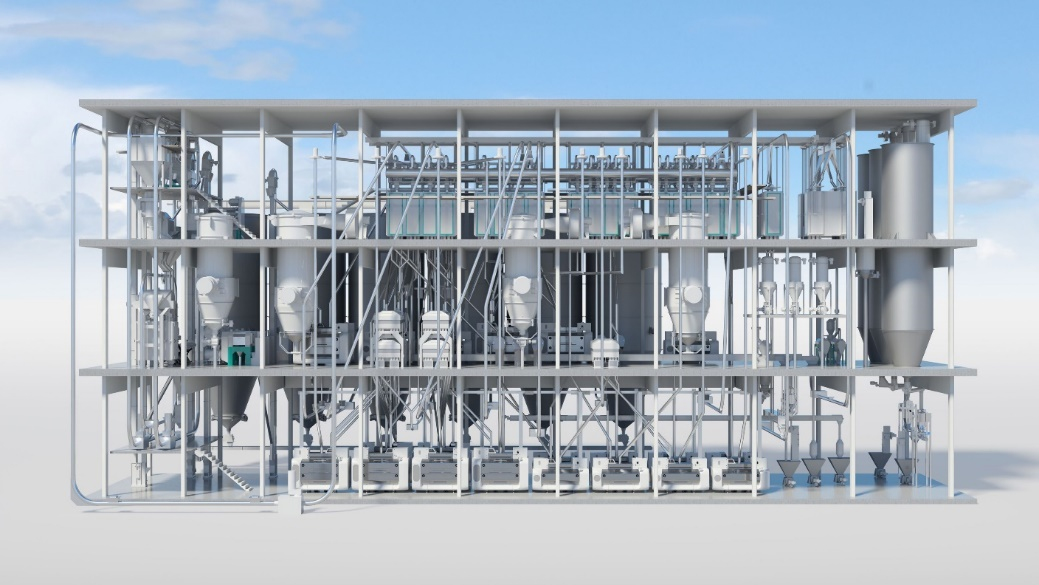
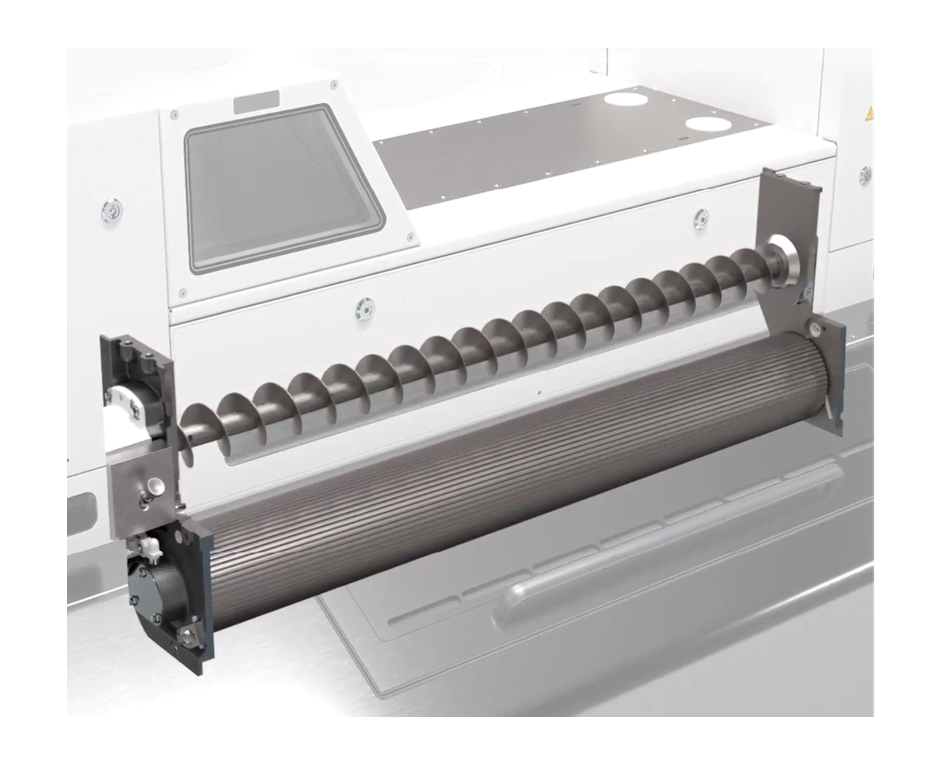
Feed control of the product is a non-linear multi-variable optimization problem
At the heart of the mill is the Arrius integrated grinding system (Figure 3). Here, the feeding module directs the incoming product to a pair of grinding rollers, where it is crushed to the desired degree in the grinding gap between the two rollers. The feeding module has two functions: distributing the product from the asymmetrically arranged inlet as evenly as possible over the width of the module, and maintaining the product flow in the grinding gap as consistently as possible, regardless of possible fluctuations in the feed and disturbances in the measurement signals. To achieve this, the feeding module is equipped with two level sensors in the feed chamber as well as a distribution screw and a feed roller, the speeds of which can be used to influence the product in the module. The feed chamber above the distribution screw serves as a buffer.
The sensor arrangement results in each of the two rotational speeds directly and nonlinearly influencing both measurement signals. From a control engineering perspective, the feeding module thus presents itself as a challenging multi-variable optimization problem: With the rotational speeds of the two rollers as manipulated variables, the goal is to simultaneously minimize fluctuations in both the "product flow" and "product distribution" variables.
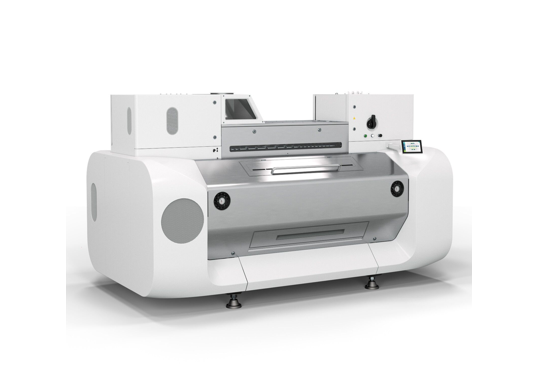
Helbling addressed this challenge by employing an optimal controller, a powerful tool in modern control engineering for solving such tasks. Optimal controllers minimize cost functions, and in this case, a combination of changes in the rotational speeds of the feeding roller and variations in product distribution proved a suitable choice. Additionally, due to the characteristics of the product and the level sensors, an observer is used (Figure 4). With its built-in system model, the observer enables a very high control performance despite uncertainties and noise in the measurement values. These uncertainties and noise arise inevitably due to the varying, imprecisely known properties of the product and the measurement technology.
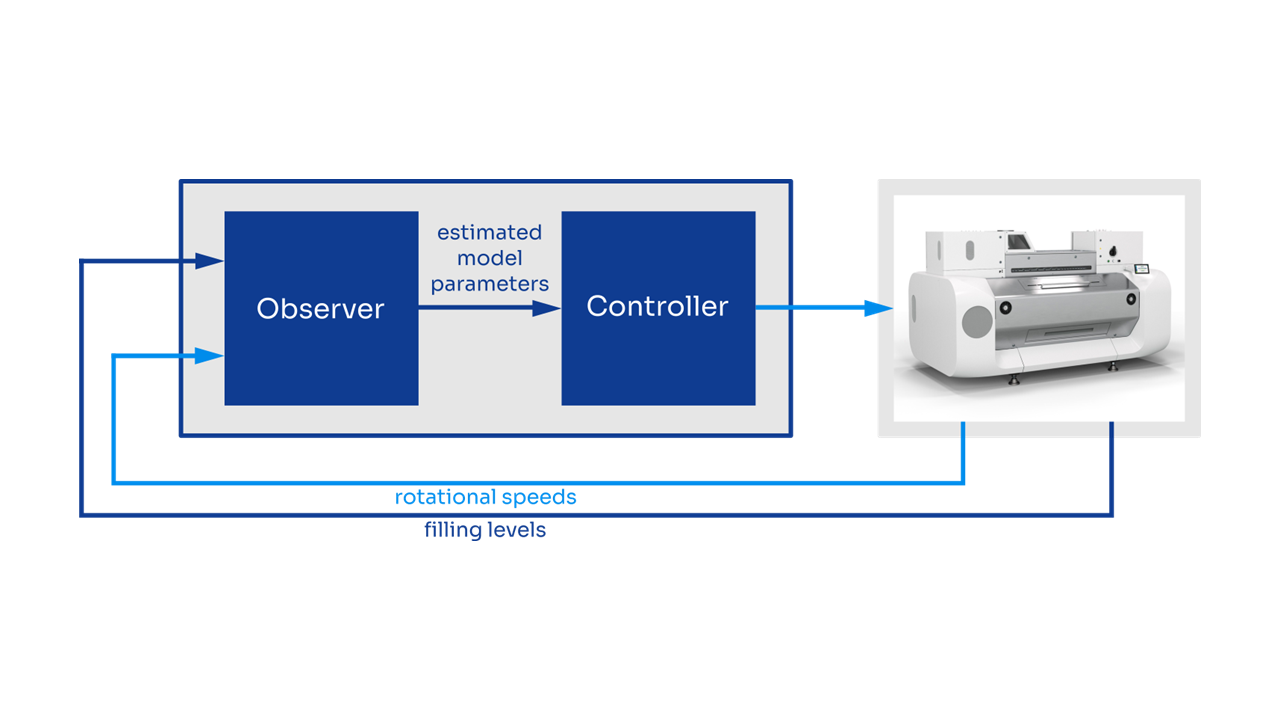
A detailed system model enables plug and play for the sophisticated controller
A particular challenge for the development team was the absence of a test facility where experiments could be conducted and ideas tested. As is often the case with large-scale plants, the required quantities of product and the associated costs are simply too high. Furthermore, certain special cases cannot be tested at all because of the inherent risks they pose to valuable equipment. Therefore, Helbling developed a comprehensive model for the behavior of the product in the feeding module. A system model developed by Bühler served as the core, with Helbling then expanding and supplementing this model in such a way that it maps the behavior of the product and feeding module with all relevant characteristics at sufficient accuracy. This allowed for realistic testing of the control system behavior and performance over an extremely wide range of possible operating situations. The system model first simulates the behavior of the feeding module in an idealized manner. Additional components then allow for the targeted replication of the non-ideal behavior of real components, product, or even disturbances.
The result of this work is a simulator that can be used in the purely virtual development environment as well as for hardware-in-the-loop (HIL) simulations (Figure 5). In the latter case, the simulator communicates with the real machine control system through the same interfaces and signals as the physical feeding module, allowing for rigorous testing of the control software in the exact manner it is intended to operate in the mill. Testing extended beyond the behavior of the controller itself, with the HIL simulator also being used to extensively examine how the control system handles real system properties (such as measurement noise), error scenarios (e.g., sensor disruptions), or extreme situations (such as a temporarily dwindling product influx), and what performance can be expected.
This comprehensive modelling of the feeding module is necessary because a real mill can only be operated with thoroughly tested software, regardless of the choice of controller architecture. The simulator can, of course, also be used to test other control strategies. For Bühler, it is a powerful tool that will continue to support the further development of the feeding module control system in the future.
It is important to note that this model should not be confused with the one used by model-based controllers and observers in their work. The latter only provides the relationship between feeding, distribution, and flow of product, as well as the sensor signals, in a highly simplified way. Its objective is not an exact representation of the processes in the feeding module, but rather the operation of the model even with the limited resources (computational power, memory) of the PLC controlling the machine.
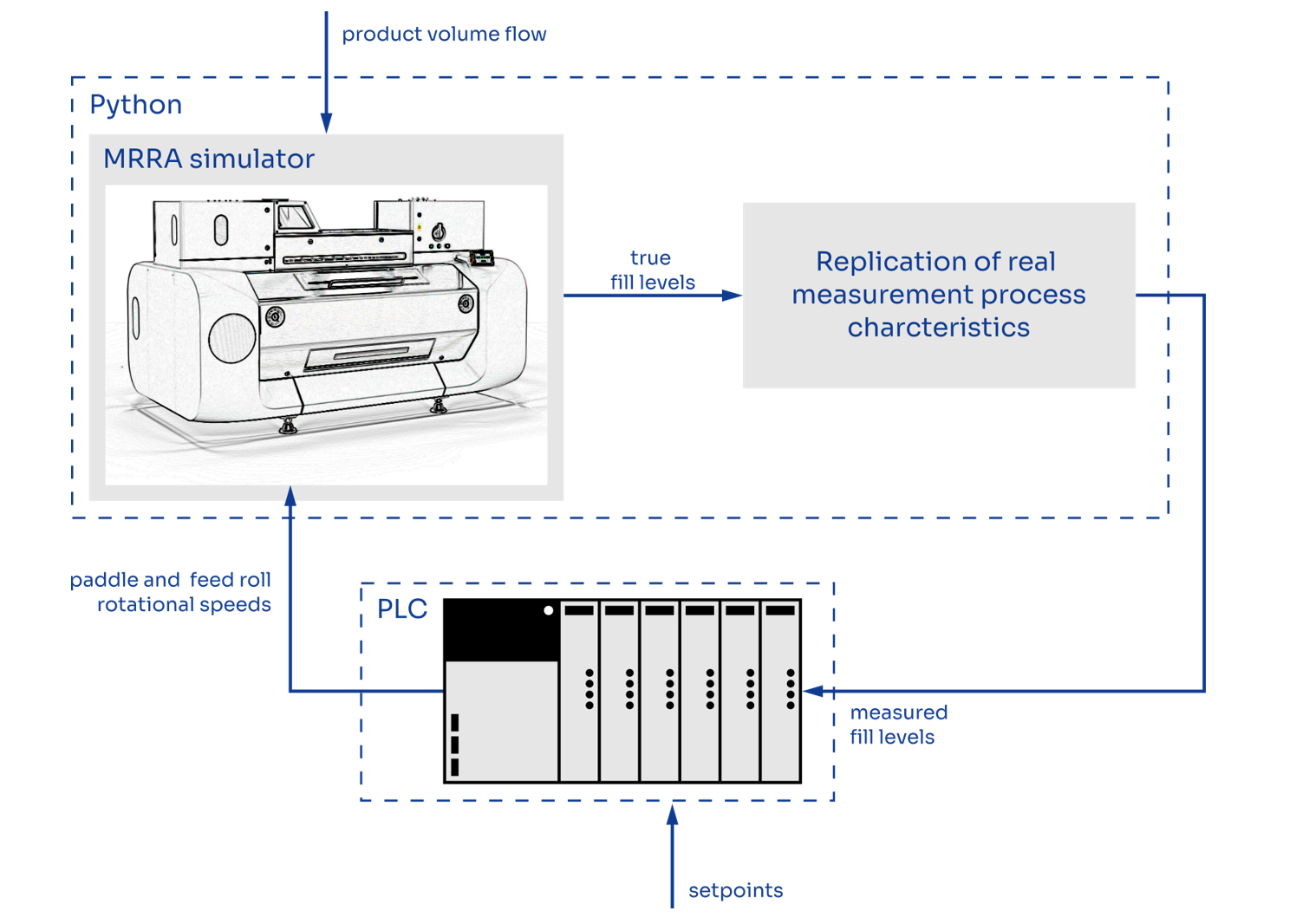
The software developed and tested in this manner passed its trial with flying colors. This affirmed the high quality of the development team's work and of the collaboration with Bühler's experts, as well as the value of rigorous testing. When installed on the first E3 mill, the controller proved to be plug and play, performing its tasks virtually flawlessly right from the start – this is by no means a given in process control scenarios. Under normal conditions, an exceptionally uniform product flow was immediately established, proving even more robust against major disturbances in the feed than initially anticipated.
Summary: A sophisticated control scheme is instrumental for autonomous and intuitive operation
With the successful development of the feeding module control system, an important building block for the realization of the E3 requirements has been implemented: The highly robust control system supports autonomous operation and high performance, which translates to a very smooth product flow. At the same time, intuitive operation allows for better and easier adjustment. Compared with a conventional control system, all of this has a positive effect on both yield and energy consumption. This use case is just one example of many: Companies from a wide range of industries can benefit from Helbling's experience and expertise in process and control technology.
Authors: Ueli Schläpfer, Michael Baumann
Main image: At the heart of the Mill E3 lie more than 15,000 data points collecting information on all aspects of the production process. Image: Bühler